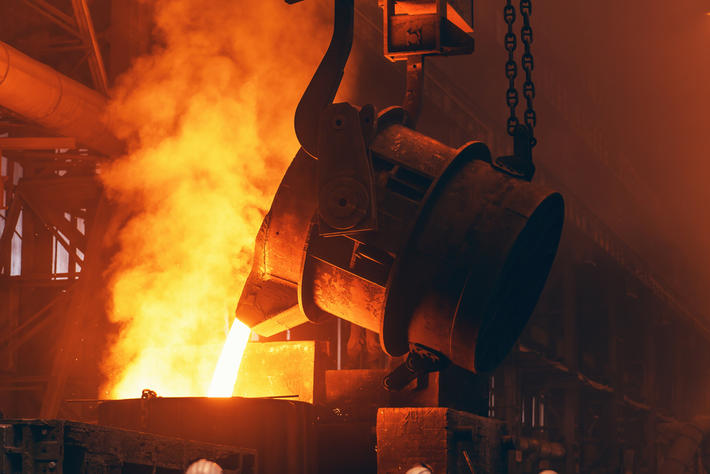
Pulverförmige Sandzusätze: Lithiumfreie Zusatzstoffalternativen für Gusseisen-, Stahl- und Aluminiumgießereien
Produktivität und Effizienz sind Eigenschaften, deren Anforderungen in der Gießereibranche stets konstant sind und ständig steigen. Gleichzeitig finden gesellschaftliche und politische Veränderungen statt. Bewusstsein und Sensibilität für ökologische Probleme sowie ständiges Engagement für den Schutz der Umwelt und die Schonung von Ressourcen stehen auf der Agenda.
Ziel von Gesellschaft und Politik ist es, kurzfristig von den klassischen und bewährten Verbrennungsmotoren abzuweichen und hin zur Elektrifizierung des Antriebsstrangs überzugehen. Im Zuge dieses Wandels gewinnt ein Rohstoff enorm an Bedeutung: Lithium.
Lithium ist ein Schlüsselbestandteil für wiederaufladbare Batterien, aber auch ein wesentlicher Bestandteil von Sandzusätzen. Die Versorgungslage und vor allem die Preisentwicklung sind schwer vorhersehbar. Darüber hinaus haben die Abbaubedingungen und der Verarbeitungsaufwand in Südamerika katastrophale Folgen sowohl für die Umwelt als auch für die lokale Bevölkerung.
Ziel ist es in diesem Zusammenhang, neue Lithium-freie Sandzusätze zu entwickeln, die den Anforderungen von Gießereien an eine nachhaltige und kostengünstige Produktion gerecht werden. Durch die enge Zusammenarbeit mit zahlreichen Gießereien konnten in den letzten 4 Jahren beachtliche Erfolge erzielt werden. Mit diesen neu entwickelten Sandzusätzen können Gießereien sowohl aktuelle als auch zukünftige Anforderungen weiterhin erfüllen.
Die wachsende Bedeutung der Elektromobilität führt zu einem drastisch steigenden Bedarf an Lithium für die Batterieproduktion. Die daraus resultierende Verknappung dieses Rohstoffs zwingt die Gießereiindustrie und ihre Zulieferer zu einer radikalen Neuausrichtung.
Gleichzeitig haben die Themen Nachhaltigkeit und soziale Verantwortung einen sehr hohen Stellenwert. Durch die Entwicklung einer neuen Generation innovativer, lithiumfreier Sandzusätze, die herkömmlichen lithiumhaltigen Sandzusätzen in nichts nachstehen, konnte die für die Herstellung der Zusätze benötigte Gesamtmenge an Lithium um 100 % reduziert werden.
Bedarf an Sandzusätzen in Gießereien
Sandzusätze werden aufgrund ihrer Zusammensetzung und Wirkungsweise grundsätzlich in 3 Gruppen eingeteilt. Die Aufgabe des Lieferanten besteht darin, der Gießerei als Einzelanwender das richtige Additiv im richtigen Zugabeprozentsatz (Sandrezeptur) für den konkreten Produktionsprozess zu empfehlen. Im Wesentlichen lässt sich festhalten, dass der Einsatz von Sandzusätzen nicht nur entscheidend für den Erhalt bzw. die Steigerung der Wettbewerbsfähigkeit ist, sondern auch für die Erfüllung der Qualitätsanforderungen an den Guss unerlässlich ist. Besonders hervorzuheben sind die guten Anti-Cresting-Eigenschaften bei hervorragender Leistung auch bei geringen Additivzugabeanteilen. Vor diesem Hintergrund ist es nicht verwunderlich, dass die Bedeutung von Sandzusätzen stetig zunimmt.
Neuartige spezielle Lithium-freie Sandzusätze für Gießereien
Je nach technologischen Anforderungen wird eine Kombination unterschiedlicher organischer und anorganischer Komponenten realisiert. Als anorganischer Bestandteil hat sich Lithium als wirksam gegen Grate erwiesen. Aus diesem Grund hat sich Lithium seit über 30 Jahren nicht nur in anorganischen Additiven, sondern auch in den neuesten Hybridadditiven als „Allrounder“ etabliert.
Unter diesen Umständen war es erforderlich, eine technisch vergleichbare, aber Lithium-freie Alternative zu finden, die Versorgungssicherheit und Preisstabilität bietet, die bei der Verwendung von Lithium-haltigen Produkten nicht mehr gegeben sind. Nach einer umfangreichen Auswahl alternativer Rohstoffe wurde eine Lösung gefunden, die zunächst auf Eigenschaften (z. B. Oberflächenqualität, Biege- oder Warmverzugsfestigkeit etc.) getestet wurde. Die ersten Tests in der Gießerei verliefen positiv, so dass das neue Produkt in Feldversuchen weiter getestet werden konnte.
Neu entwickelte Sandzusätze haben sich in vielerlei Hinsicht bewährt:
- deutliche Reduzierung von Gussfehlern, die zu Nacharbeit oder Ausschuss führen,
- Reduzierung oder sogar Verzicht auf den Zusatz von Spezialsanden,
- unter bestimmten Voraussetzungen ist es möglich, einen Guss ohne Lackierung herzustellen,
- bessere Metallbearbeitbarkeit mit längerer Werkzeugstandzeit,
- Möglichkeit, den Einsatz von Trennmittel zu reduzieren,
- hervorragende Fließfähigkeit der Kernformmasse bei guter Definition der Geometrien,
- Additive für Aluminiumgießereien, die das PUCB-Verfahren (PhenolicUrethaneCold Box) anwenden, mit dem Ziel, die Schmutzbarkeit des Sandes zu verbessern,
- Additive, die die Biegefestigkeit (für Kerne/Formen) für die CB-, Resol-CO2- und Resol-Methylformiat (MF)-Prozesse erhöhen und so eine Reduzierung des Bindemittels ermöglichen.
Höhere Produktivität dank saubererer Anlagen (Phenol-Urethan-Kühlbox)
Trotz der Anwendung eines nachweislich wirksamen Trennmittels kann es insbesondere in der Nähe der Schüsse innerhalb kürzester Zeit zu einer Ansammlung von harzigem, mit Sand vermischtem Pech kommen.
Bis zu einem gewissen Punkt wird diese Hinterlegung in der Seelenbox akzeptiert bzw. toleriert. Nach einer gewissen Anzahl an Zyklen ist dennoch eine Produktionsunterbrechung zur Reinigung notwendig. Durch die Zugabe des Additivs wird sowohl der Zeitverlust im Vergleich zur Standardproduktion als auch die Pechbildung im Kernkasten deutlich reduziert. Nach 117 Zyklen ohne Reinigung des Kernkastens und ohne Betriebsunterbrechung konnte der Auftrag des Trennmittels drastisch reduziert werden, es kam zu keiner Verharzung und eine Reinigung der Entlüftungsöffnungen war nicht notwendig.
Reduzierung der Gesamtprozesskosten
Im Bereich der Cold-Box-Fertigung bietet der Verzicht auf Lackieren wohl die größte Chance, die Produktivität zu steigern und mit Zusatzstoffen eine hohe Qualität der Gussteile sicherzustellen. In den letzten Jahren haben wir in Zusammenarbeit mit den wichtigsten Gießereien daran gearbeitet, den Lackierprozess nach Möglichkeit zu vermeiden. Dieses Ziel konnte dank der neuen Additive bei zahlreichen Gussteilen erfolgreich erreicht werden. Die wirtschaftliche Bewertung des konventionellen Verfahrens berücksichtigt die Gesamtkosten der Kernformmasse, die Kosten für die Putze, etwaige Zusatzstoffe, etwaige Spezialsande, den Verwaltungsaufwand des Lackierprozesses und die Energiekosten für die Trockenöfen.
Dadurch erwies sich das lackfreie Verfahren als deutlich wirtschaftlicher. Bei der Berechnung des Einsparpotenzials müssen künftig auch Steuern auf das erzeugte CO2 berücksichtigt werden. Abhängig von der Struktur des Ofens und den Oberflächen der Kerne/Formen kann dieses Element bei einem Einsatz von ca. 100 Tonnen zu zusätzlichen fünfstelligen Euro-Kosten führen. Wasserputz pro Jahr, ab 2025.
Kosteneinsparungen durch Ersatz von Spezialsanden
Unter Spezialsanden versteht man sowohl natürliche Mineralsande als auch Sinter- und Gussprodukte, die in Granulatform hergestellt werden. Sie zeichnen sich gegenüber Quarzsanden insbesondere durch ihre geringere Wärmeausdehnung aus, die im Temperaturbereich von 20 bis 800 °C deutlich geringer ist.
Im Gussprozess werden Spezialsande wie Chromitsand, keramische Hohlkugeln, Andalusit- und Feldspatsande verwendet. Die Zugabemengen (in der Regel 30 bis 100 %) variieren stark je nach Ihrem spezifischen Bedarf.
Spezialsande sind ein wirksames Mittel gegen Gussfehler mit geringer oder keiner Gas- und Geruchsemission. Sie sind bis auf wenige Ausnahmen nicht verwertbar/trennbar und verursachen hohe Entsorgungskosten. Ab einer gewissen Anreicherung kann sich der Einsatz von Spezialsanden negativ auf das Grünsandsystem auswirken. Darüber hinaus können die Kosten für Spezialsande stark schwanken. Die Leistungsfähigkeit von Spezialsanden ist nach wie vor unbestritten. Allerdings muss man sich fragen, ob die Wahl des Formmaterials sowie die verwendeten Mengen für die Zwecke sinnvoll sind. Zu oft werden Kosten in Kauf genommen, weil keine Alternative erkennbar ist, um die gewünschte Qualität zu erreichen.
Erhöhte Festigkeit bei Prozessen mit RESOL-CO2 / RESOL-Methylformiat
Typischerweise erfordert die Zugabe herkömmlicher Additive eine Erhöhung des Bindemittels. Die Entwicklung eines neuen, patentierten Additivs ermöglicht es, die Festigkeit der kernbildenden Mischung gezielt zu erhöhen. Von besonderem Interesse ist es für Bindemittelsysteme wie RESOL-CO2 / RESOL-MF, die zur Erzielung der gewünschten Biegefestigkeiten hohe Anteile an Additiven erfordern, gleichzeitig aber durch die hohe Viskosität der Bindemittelsysteme begrenzt sind.
Durch die neu entwickelte Additivtechnologie können Sie die Widerstandsfähigkeit erhöhen und gleichzeitig die Fließfähigkeit verbessern. Auch die systemtypische verminderte Feuchtestabilität und die Beständigkeit gegenüber Wasserputzen können durch diese Zusätze verbessert werden.
Der festigkeitssteigernde Effekt ist ein Ergebnis der erhöhten Fließfähigkeit der Kernformmischung (Physik) und der Vernetzungseigenschaft (Chemie) des Additivs. Daraus ergeben sich folgende Vorteile für den gesamten Prozess:
- Vermeidung von Gussfehlern, Reduzierung der Bindemittelmenge,
- die Verwendung wasserbasierter Farben erlauben oder erleichtern,
- Verbesserung der Fließfähigkeit und geometrischen Definition (in der Kernbildungsphase),
- Verbesserung der Erdbarkeit nach dem Gießen und Ausrüsten,
- Wegfall von Verstärkungen in den Kernen (z. B. Eisenstangen),
- Erhöhung der Haltbarkeit von Kernen,
- robusterer Produktionsprozess, d. h. ein weniger empfindliches System bei Prozessschwankungen.
Abhängig von dem Gesamtziel, das Sie erreichen möchten, kann dieser Aspekt durch die Menge an Bindemittel und/oder Zusatzstoff gesteuert werden. Dies eröffnet dem Anwender bisher nie dagewesene Möglichkeiten, spezifische Anforderungen mit lithiumfreien Additiven zu realisieren.
Additive für Cold-Box-Prozesse zur Verbesserung der Schmutzbarkeit von Pur-Aluminiumgussteilen
Um das Ausschütteln und die Verschmutzungsfähigkeit zu verbessern, neigen Gießer dazu, die Harzmenge zu reduzieren und/oder gröbere Sande zu verwenden. Geringe Bindemittelmengen sind auf den ersten Blick ein ökonomisch und ökologisch sinnvoller Ansatz. Durch die reduzierte Bindemittelzugabe verbessert sich zwar die Schmutzbarkeit, allerdings wird die Handhabung der Kerne kritisch. Meistens verbleibt trotz aller Bemühungen der gesamte Kern oder ein großer Teil davon nach dem Gießen und Erstarren im Gussstück. Folglich müssen die Reste des Kerns selbst nach dem Ausschütteln auch mit großem Aufwand entfernt werden. Die schlechten Kneteigenschaften von CB-gebundenen Kernformstoffen verringern daher die Produktivität von Aluminiumschmelzprozessen erheblich.
Hier bietet das neue ausschlagfördernde Additiv einen entscheidenden Vorteil: Praxistests haben gezeigt, dass die Entfernungszeit von Kernrückständen (Finishing) um über 30-50 % verkürzt werden kann.
Neben dieser deutlichen Produktivitätssteigerung bietet die neue Additivgeneration folgende Vorteile:
- relativ geringer Zusatz von Zusatzstoffen (ca. 0,5-1,5 %),
- deutliche Verbesserung der Entschmutzung,
- Möglichkeit der teilweisen Reduzierung des Bindemittels,
- anorganischer Zusatzstoff.
Pulverförmige Additive für lithiumfreie Sande für Gießereien
Die Entwicklung der Antriebstechnik im Automobilbereich hin zur Elektromobilität verdeutlicht die Bedeutung der Batterieproduktion, aber auch die daraus resultierende Abhängigkeit vom Rohstoff Lithium. Die Lieferungen waren durch enorme Preissteigerungen gekennzeichnet. Darüber hinaus ist es wichtig, die katastrophalen Auswirkungen auf Menschen, Tiere und die Umwelt in Bergbaugebieten im Auge zu behalten. Da Lithium seit über 30 Jahren als wesentlicher Bestandteil in vielen Sandzusätzen eingesetzt wird, wurde eine technische Alternative entwickelt.
Die neue Technologie, bei der Lithium-freie Additive zum Einsatz kommen, bietet Gießereien wichtige Vorteile:
- Steigerung der Produktivität durch Verbesserung der Schmutzbarkeit von Aluminiumgussteilen,
- Einsparung von Rohstoffkosten durch den Ersatz teurer Spezialsande,
- Prozesskosteneinsparungen und gesteigerte Produktivität durch kürzere Reinigungszyklen,
- Einsparung von Prozesskosten, Energieeinsparung durch einen Produktionszyklus ohne Lackierung.
Quelle: In Fonderia – ll magazine dell’industria fusoria italiana